Alarm Clocks, Ice Scrapers
and 40 laps a day...
March 28th, 2024
We take our lifetime guarantee VERY seriously and we are well-known as the most uncompromising set of perfectionists you’re ever going to meet! So it goes without saying that the testing for our prototype bikes would be absolutely brutal for both man and machine!
First comes FEA (Finite Element Analysis) a computer simulation of the most extreme forces that the frame will experience in use so we can provide the lightest possible design for a given set of loads and boundary conditions. So with this theoretical assurance, we set about the practical, only after the most exhaustive testing in the field would we be ready to send a frame with Atherton on its downtube to the most rigorous test-lab in the world at EFBE. More about the lab tests in part 2…but firstly dawn till dusk and Dyfi to “Down under” most of the Athy Bikes and Dyfi Crew got involved with thrashing our prototype bikes as hard as they could!
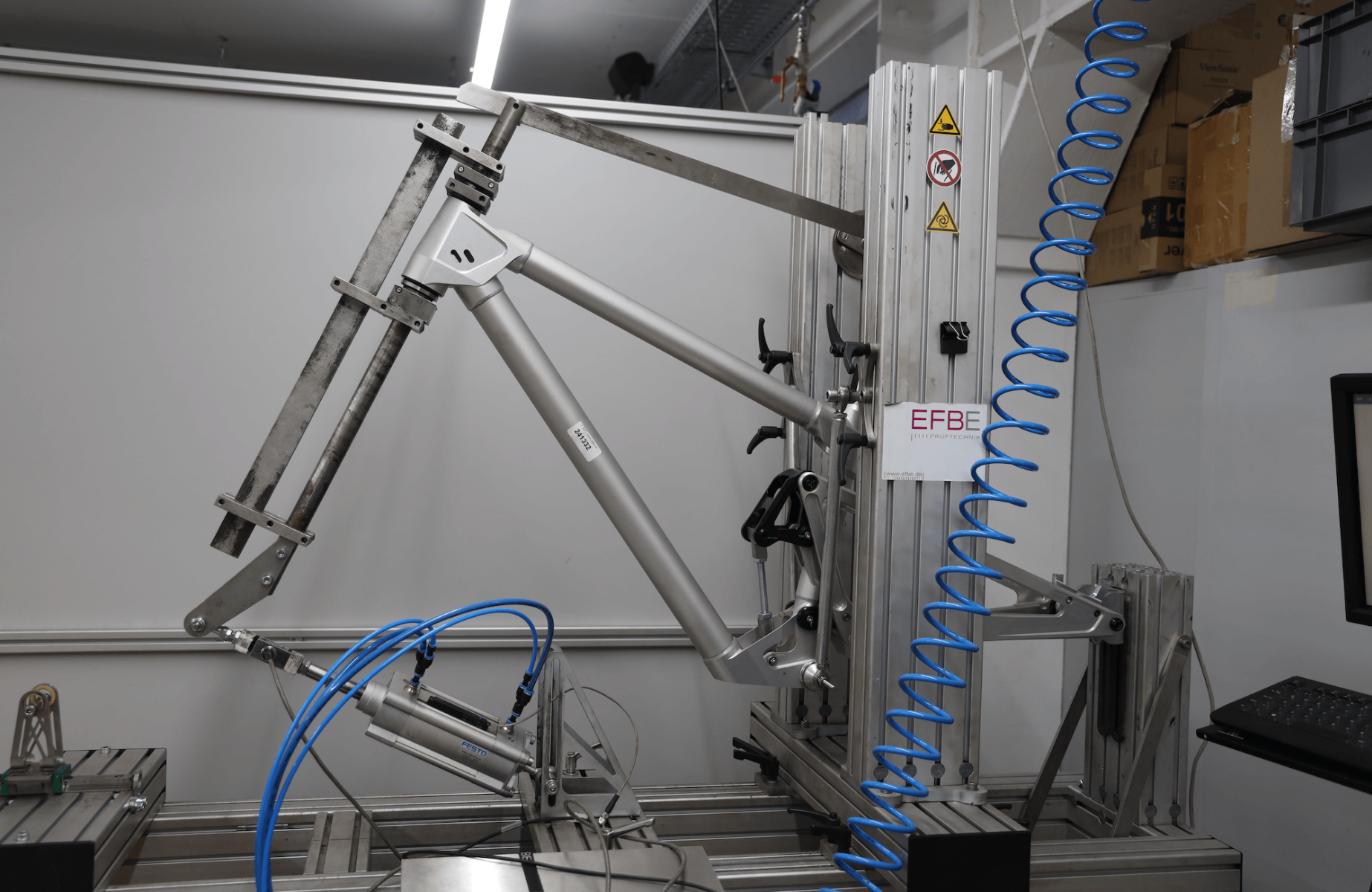
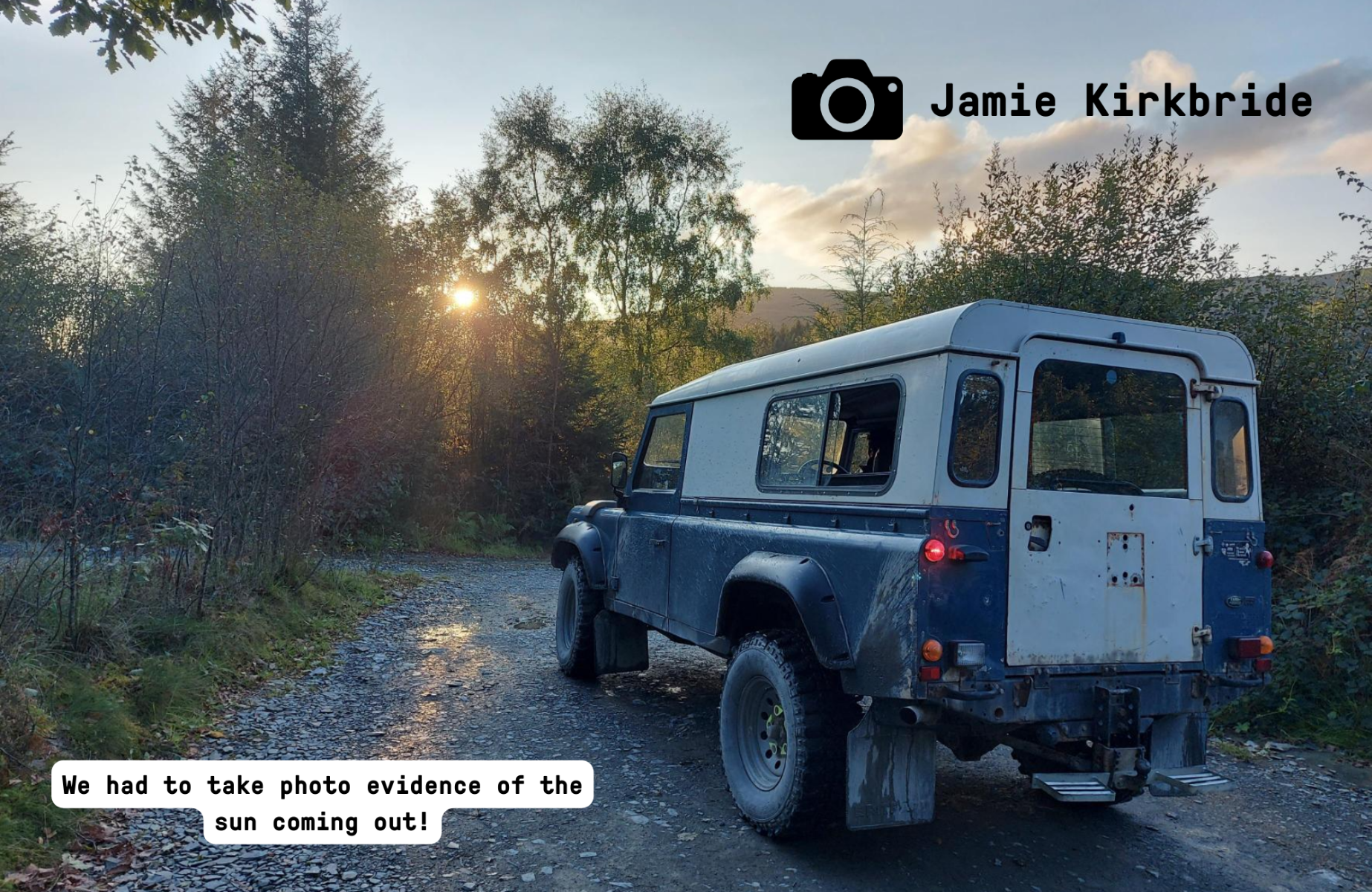
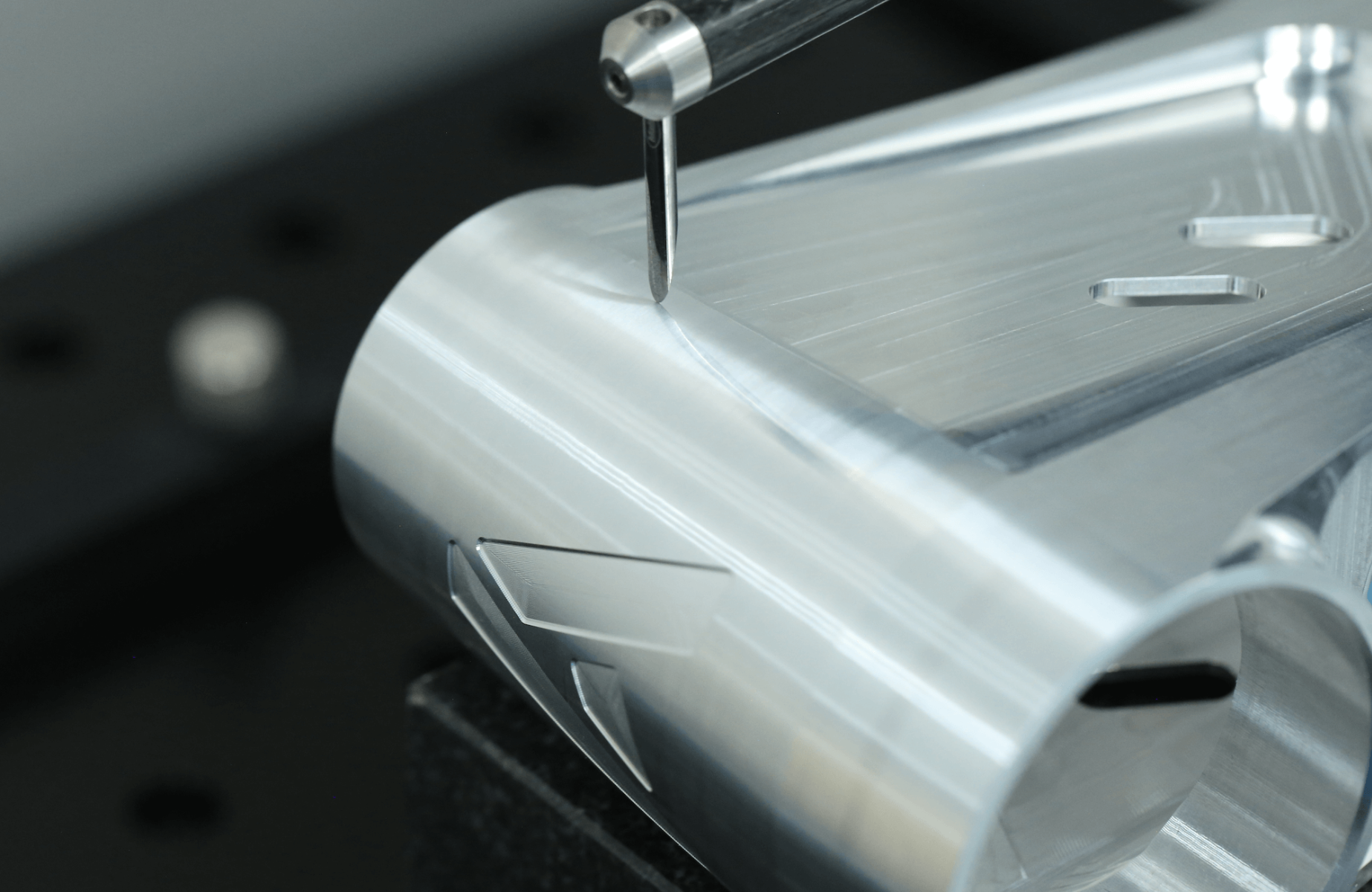
Field testing S170: Dark till dark, rain or shine, field testing, 40 laps a day for months…
We operated three shifts, Shift 1 was “before work” daybreak till office hours, Shift 2 was 8.45 am to 1 pm (often the dig crew) and Shift 3 started at 1 and ran until dark. 40 laps a day is over 4 times the average bike park user and we were lapping some of the most abusive trails in the UK, we needed those shifts because one rider simply couldn’t cope with the physical abuse!
Lead machine Operator Jamie Kirkbride said “In a word it was grim! Cold, wet, dark, muddy and repetitive. Breakfast most days was a pack of Monster Munch and a Red Bull in the back of the Landrover,I got good at the top section of racetrack, definitely Type 2 fun.”
Dan Atherton said “Testing at this level was driven by the engineers and the need to rack up a huge amount of hours on the bike. The thing that stood out for me was how intense things got, we had a relatively short window and we knew that we had to get it right. Our Head Designer Rob Gow was driving the whole testing schedule, he’s the one who knew the importance of speeding up the process of time by getting in loads of laps, and with riders at different levels so it was full company involvement with dig crew taking time out of digging, Dan Brown and the production and engineering boys, coming over before work and Gee, Charlie, me and a couple of others flat out going as fast as we could! It made for pretty heavy days – we were pissed off with Rob the whole time J It’s what makes him and Scott and Will so good; that ability to focus on what’s important and what needs to be done, nothing else.”
In the Dyfi, we carefully selected a combination of trails to ensure all natures of abuse were covered off, inside and outside of the Park. Different aspects of the testing required different tracks or features to demonstrate the full range of possibilities so depending on what we were looking for we’d focus on different parts of the track.
Dan said “We ran part of the compliance feedback around corners with plenty of support; a good steep berm so you could push as hard as you can without worrying about the tyres; the only thing you need to think about is the flex of the bike. Aluminium is inherently stiffer than carbon so we were testing “is the rear end pliable enough?” At P1 (prototype 1) stage the major feedback, especially from the fast guys was that the rear end was too stiff, so for P2 we made it more compliant, and the testing started again!!”
Suspension came to the fore on the rough Racetrack while geometry was key on longer rides outside of the park. We learnt a lot in so many areas - for example on sound-deadening; it’s a lot harder to get right on the aluminium bike than the A-Range bike as any sound is amplified through the tubes. The mix of World Cup racers, local free-riders and novice riders ensured we covered all the bases from race pace laps to flat landings and more cases than you could ever dream of! All those different skill levels were super important in fine-tuning the finished ride.
We managed our P1 testing in the summer when the long hours were relatively easy to achieve. But P2 testing took us into the depths of winter. There are two drawbacks there (on top of freezing the riders to death) one is that you’re limited by daylight hours (riding with lights just isn’t abusive enough) and the second is that testing in the wet is great for loads of reasons (particularly all the bearing and hardware tests) but even riders like Gee, Charlie and Dan can’t push as hard as they would in the dry.
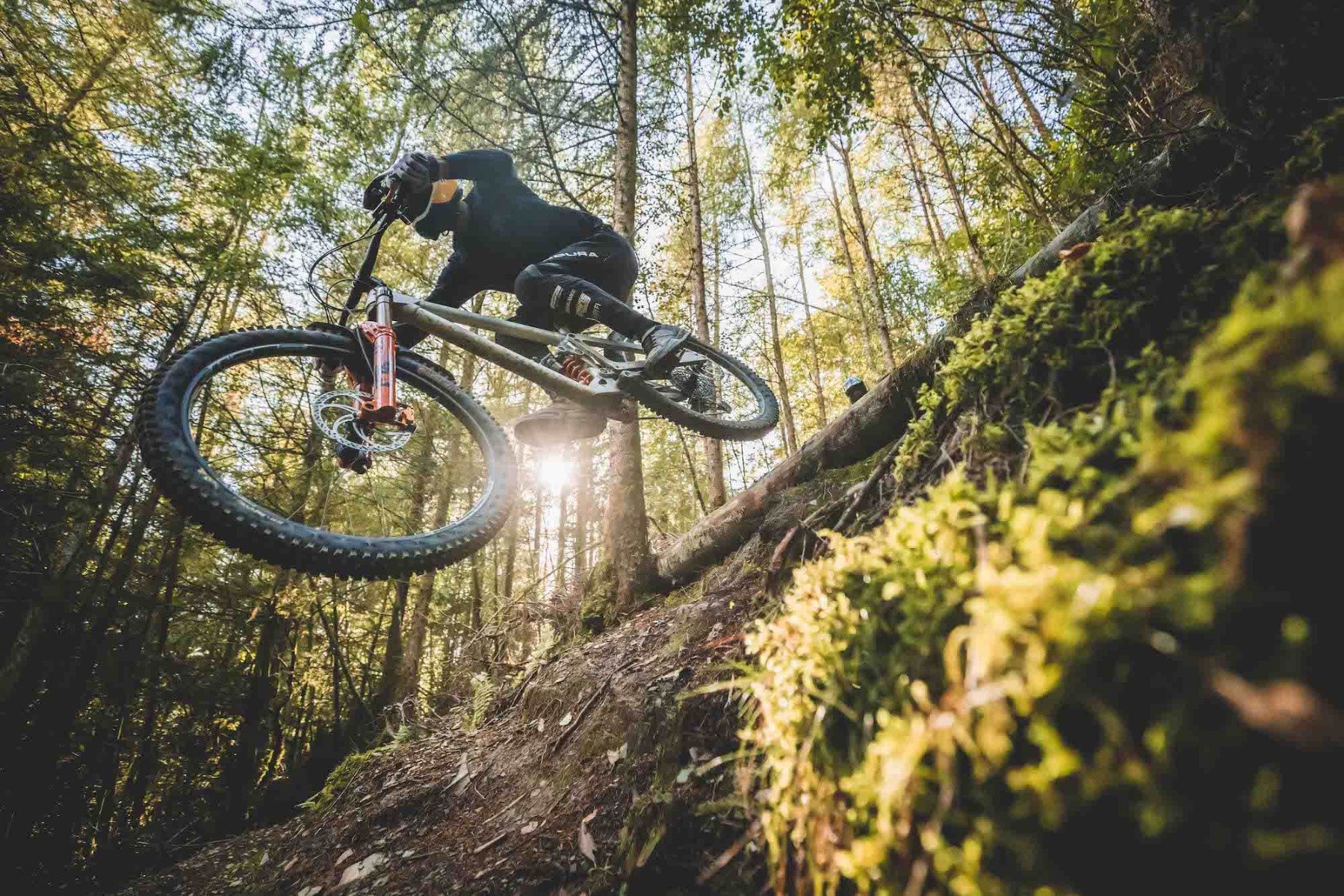
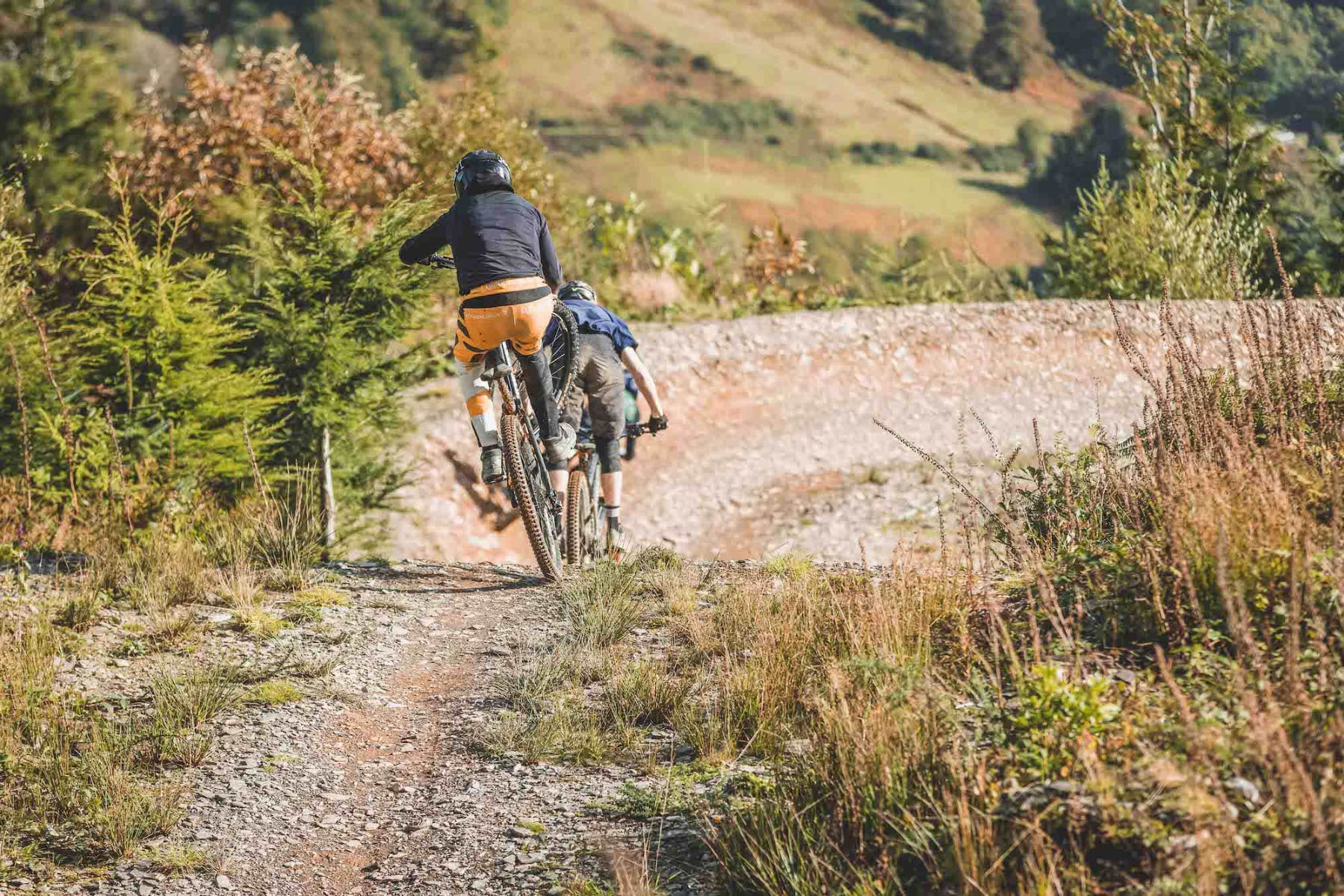
So we found summer on the other side of the world (our Hemispheres film is well worth a watch) sending a couple of prototypes out to New Zealand. Charlie Hatton, Jim Monro, Dennis Luffman and our head race team technician Ben Lovell took full advantage of the heat and the dust of Queenstown and beyond – huge jumps and super fast tracks gave a different perspective while their wild rides also started to raise awareness of the bike…
Dan said “It was super useful for me to see first-hand that huge variation in ability and styles and the different demands that brought with it. For me the S.170 is an amazing ride, it’s great fun in the park but comes into its own on the Enduro big mountain stuff, where you feel the benefits of 170mm of travel. What struck me most though was that the testing showed that the bike could pushed by everyone; World Cup racers to near novices – we were all riding it as hard as a DH bike! The whole way through everyone was super excited for the whole range…
Break out quote “Testing the S.170 in NZ was so sick, it fills you with confidence and just wants to go fast. It's heaps of fun, literally a mini DH bike!” Charlie Hatton, Reigning Downhill World Champion
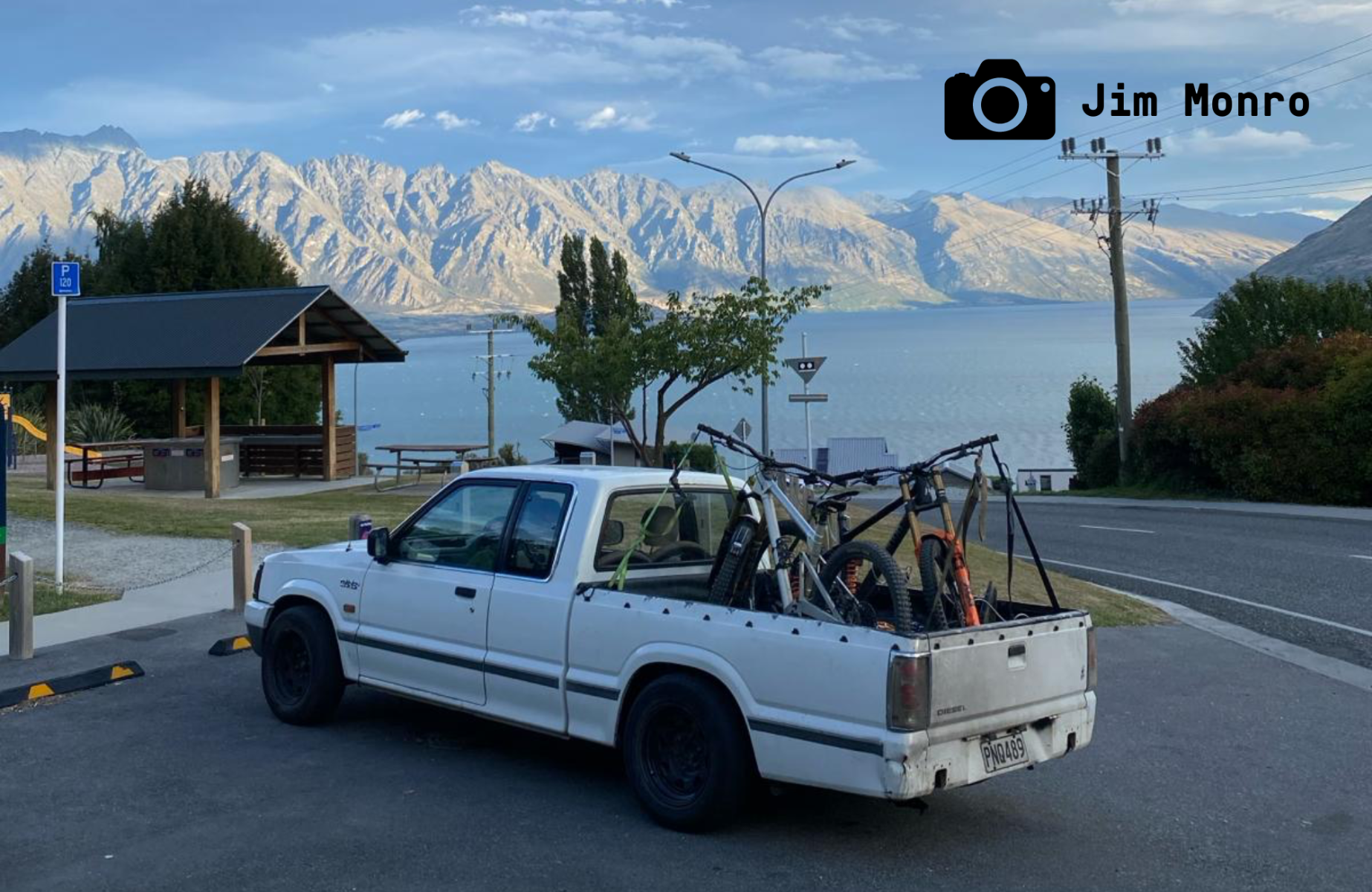

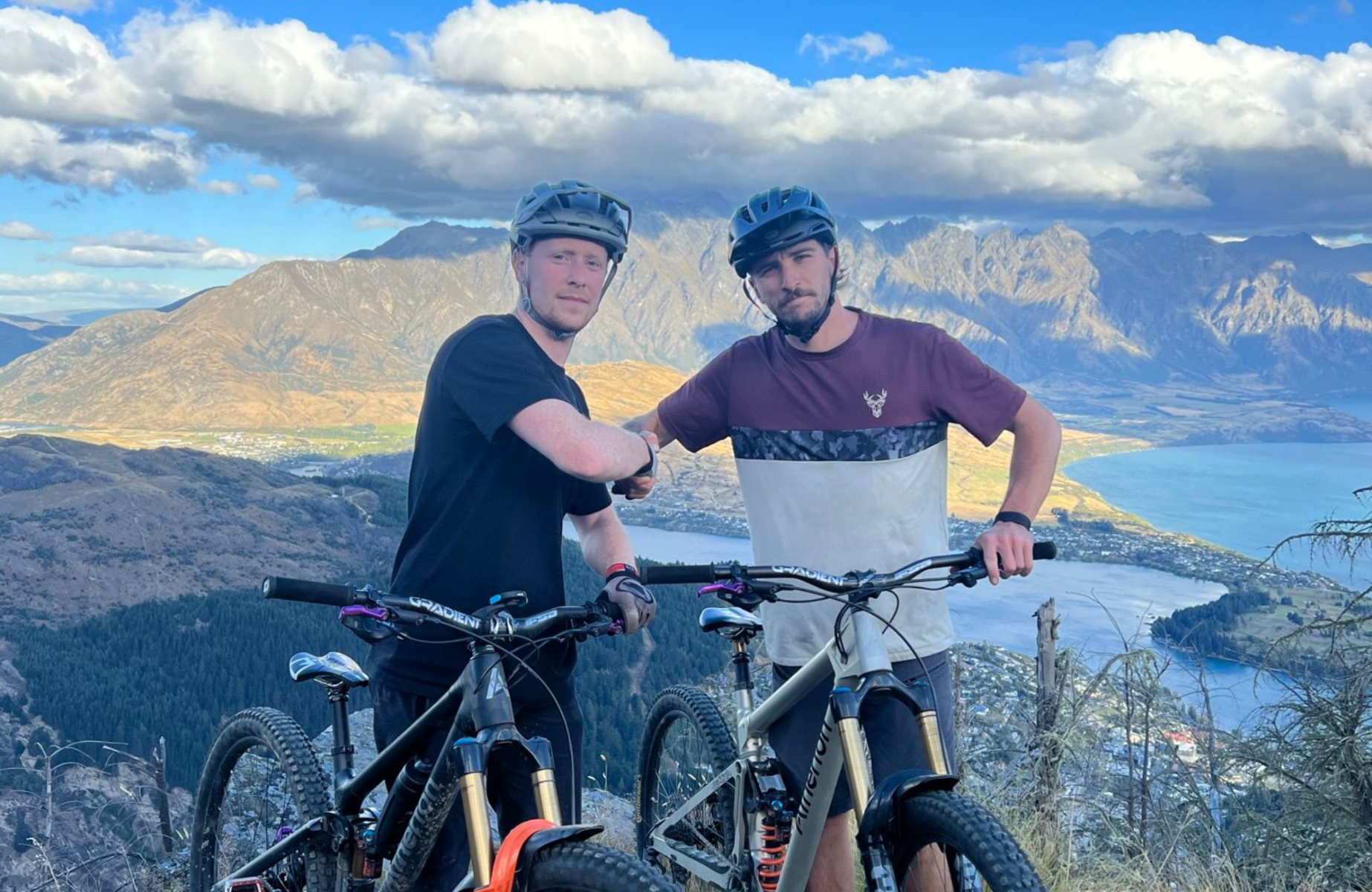
Remarkably no riders were (seriously) hurt in the testing of this bike.. but the boys left a trail of destruction... parts were harmed in the making of this bike (Dyfi Section) listed here!
❌ | 10 Rear wheels, 3 front wheels |
❌ | 10 sets of brake pads |
❌ | 7 Tyres, 3 Front Tyres |
❌ | 2 Disc Rotors |
❌ | 6 gear cables |
❌ | 5 rear mechs |
❌ | 6 chains |
❌ | 4 headsets |
❌ | 6 bottom brackets |
❌ | 3 sets of forks |
❌ | 7 shocks |