Blog - 29 November 2024
Building an Atherton in Aluminium
We've always had the ambition to make Atherton Bikes available for more riders
RG: From the very beginning, before the company was even an entity, we shared an ambition to make Atherton bikes available to a lot more riders, not everybody can justify a high performance, carbon and titanium bike. We wanted to continue to offer all the benefits that we hold dear on sizing, strength and ride performance and to include the learnings from five award-winning years such as our established preferences on geometry and ride feel. We were looking for a solution that would lower costs but equally important this range would bring a more everyday, lower maintenance kind of vibe … “Just chuck it in the van and go!”
We were determined that this new bike would feel like an Atherton but it would be a different kind of Atherton, the different material ensures that. This entire range would be fun to ride as you’d expect, even more rugged but more accessible than our A Range bikes.
Gee said it well “We were looking for a real alternative to our flagship A-range but we’d only ever produce bikes that we’d be proud to call an Atherton. It was essential that we’d be excited to ride the S170 – but comparing anything to the A.170 is a really big ask, both Dan and I rate the A170 our favourite bike ever, but the S.170 is a lot of fun and can take everything that you can throw at it”.
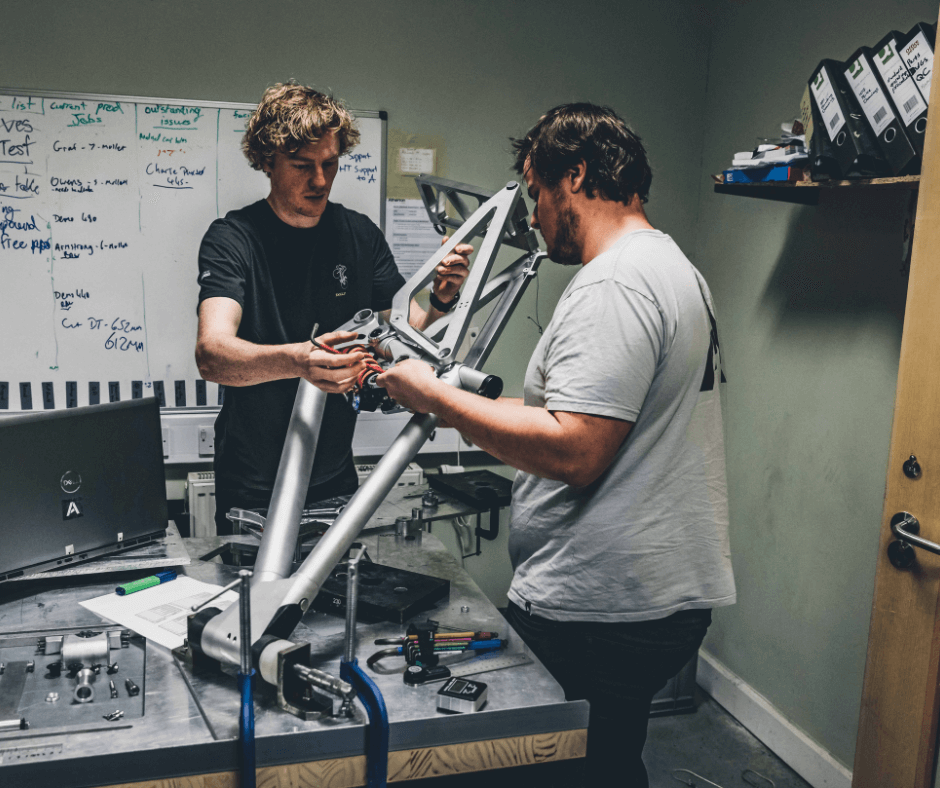
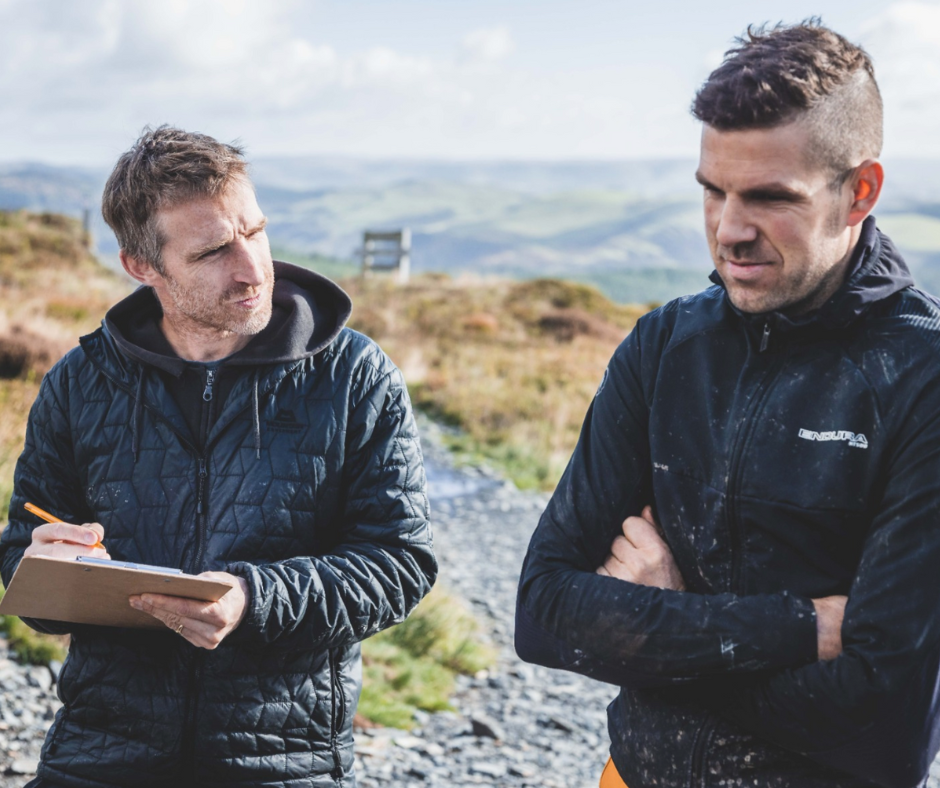
There have been so many questions about how we got to the geometry and ride characteristics of the bike, but it turns out that was the easiest part of the whole equation. We are launching the S-range with just one model, the S170 and that mirrors the geometry of the A170 (Dan Atherton’s absolute dream bike) Moving from DW6 on the A range to DW4 on the new S Range Dave Weagle nailed the kinematic on the first attempt.
On the other hand, developing a production process from the ground up was a massive undertaking. Our design brief from the board was very clear that there could be no compromise on strength, sizing or our target price. We agreed that a small hit on weight and customisation was permissible and this formed a very clear brief for a real product.
We started with a blank piece of paper. We’d learnt a lot through our additive manufactured (AM) range but consciously didn’t want to tie ourselves down or start from an assumption that we’d use lug and tube. We looked at everything from welding to binder jet and the latest advances in AM, combinations of forging, and extruding… we cast the net as wide as possible and came back right to lug and tube!! But in a different material and using a different manufacturing process. I was a bit disappointed at first but we’d stuck to very methodical decision-making based on engineering principles so I was sure we’d reached the right result.
So we had a direction; lug and tube construction, in aluminium.
But there were still some big questions to overcome! How to perfect the lugs for one…Additive manufacturing allows us to place titanium exactly where we want it, in pretty much any shape, how could we do this with a cheaper material and using different processes to achieve similar results? The answer was CNC machining. Although this is a very established process there is still a huge amount of innovation going on. There’s a real art to achieving your desired geometry at the right cost and it was only possible through close collaboration with our technical partners and taking a rather leftfield approach! The results are a very honest aesthetic that we are very proud of. Every shape has a function and a story behind it, strength above looks governed by every choice.
Technology
Bonding rather than welding frees up the materials we can choose. 7075 aluminium is about 80% stronger than 6061 usually used in bike manufacture and avoids inherent welding issues like distorted, heat-affected zones. We ride at Dyfi Bike Park pretty much every weekend and we chat to people on every uplift.
So we’re very aware of the amount of competitor frames getting warrantied and determined to avoid that for our bikes. Like our A Range bike, the S.170 is designed around an Infinite Life principle. This means that our frames can be subjected to forces experienced in the most extreme riding situations an infinite number of times and never start to fatigue (metal failure after repeated loading). We use double lap joints carried straight over from A Range, a key part of the strength of our bikes and constant wall thickness drawn Aluminium tubes.
There’s nothing radical in these separate elements but by bringing them together in a genuinely unique combination we knew we’d only discover our limits through the most rigorous testing, luckily we have the perfect testing place and perfect testing crew. It's tough but you only know how good something is when you can break it. And so we set about trying to break the product we were so proud of creating… we created the ultimate horrible run and rode in an absolutely brutal regime lapping combinations of the most brutal trails, 40 laps a day until we found a weakness. And then we’d regroup and go again. And again! World Cup racers, local free-riders and novices ensured we covered all bases, and upped the number of cases considerably!
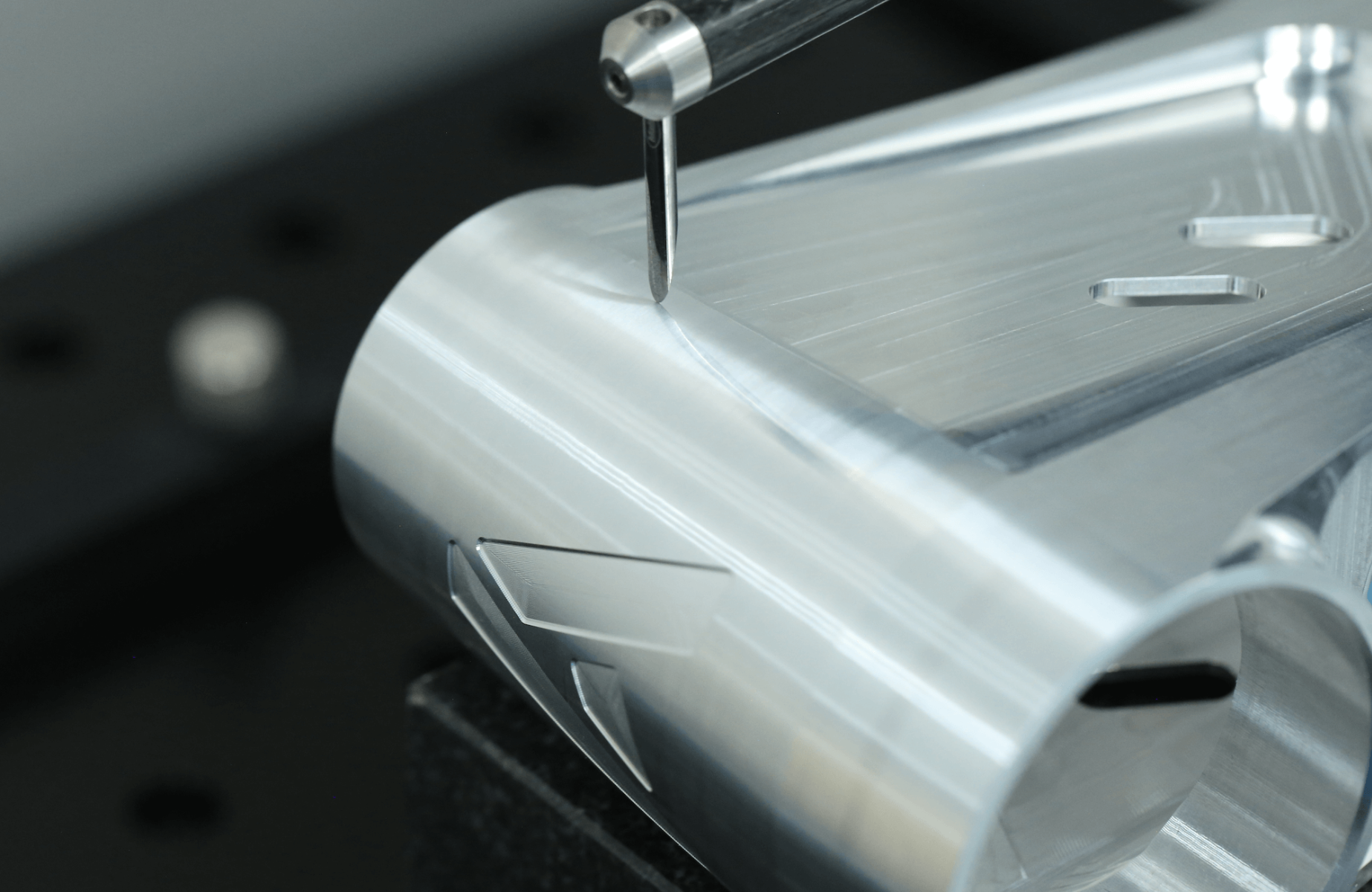
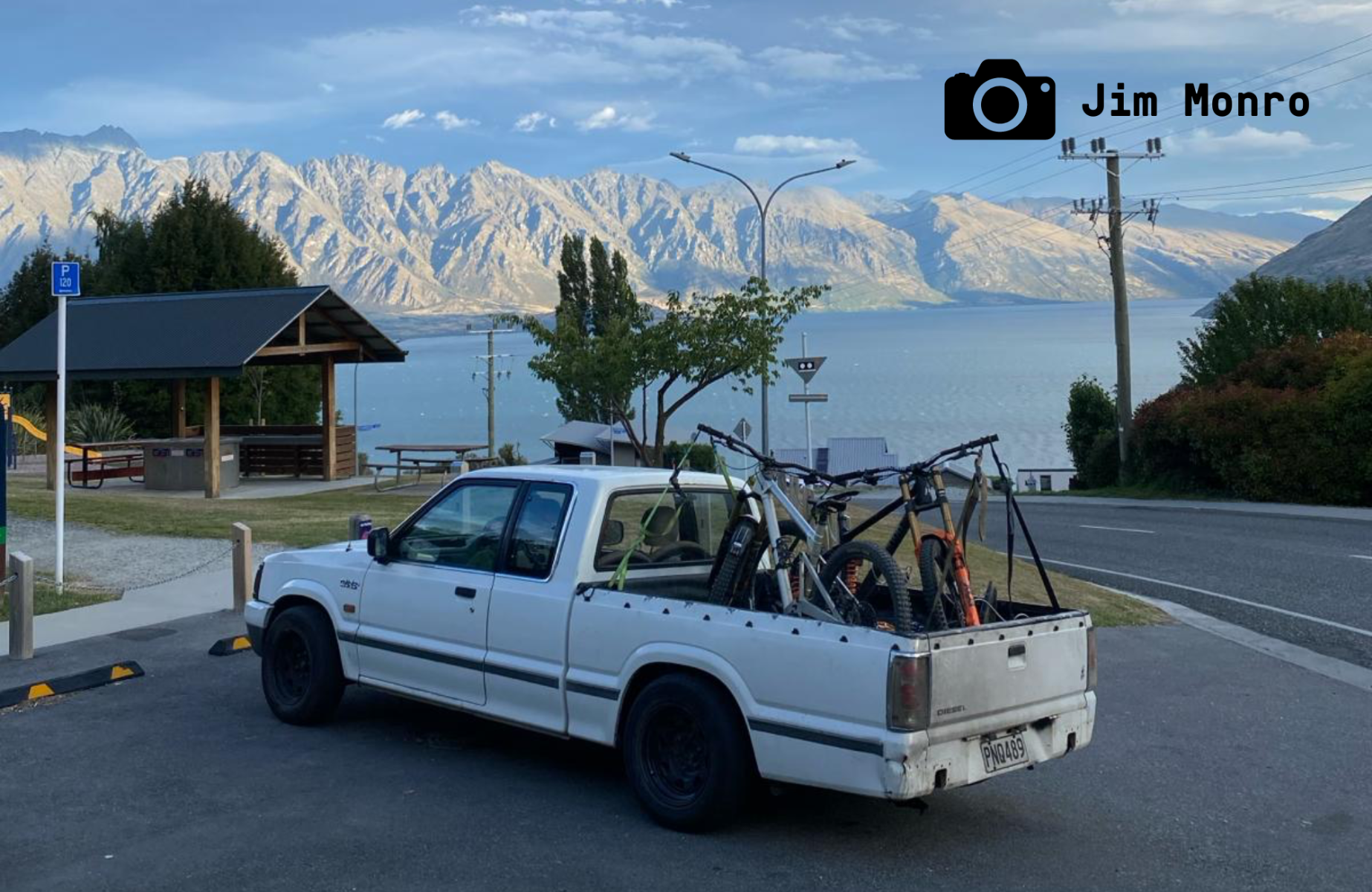
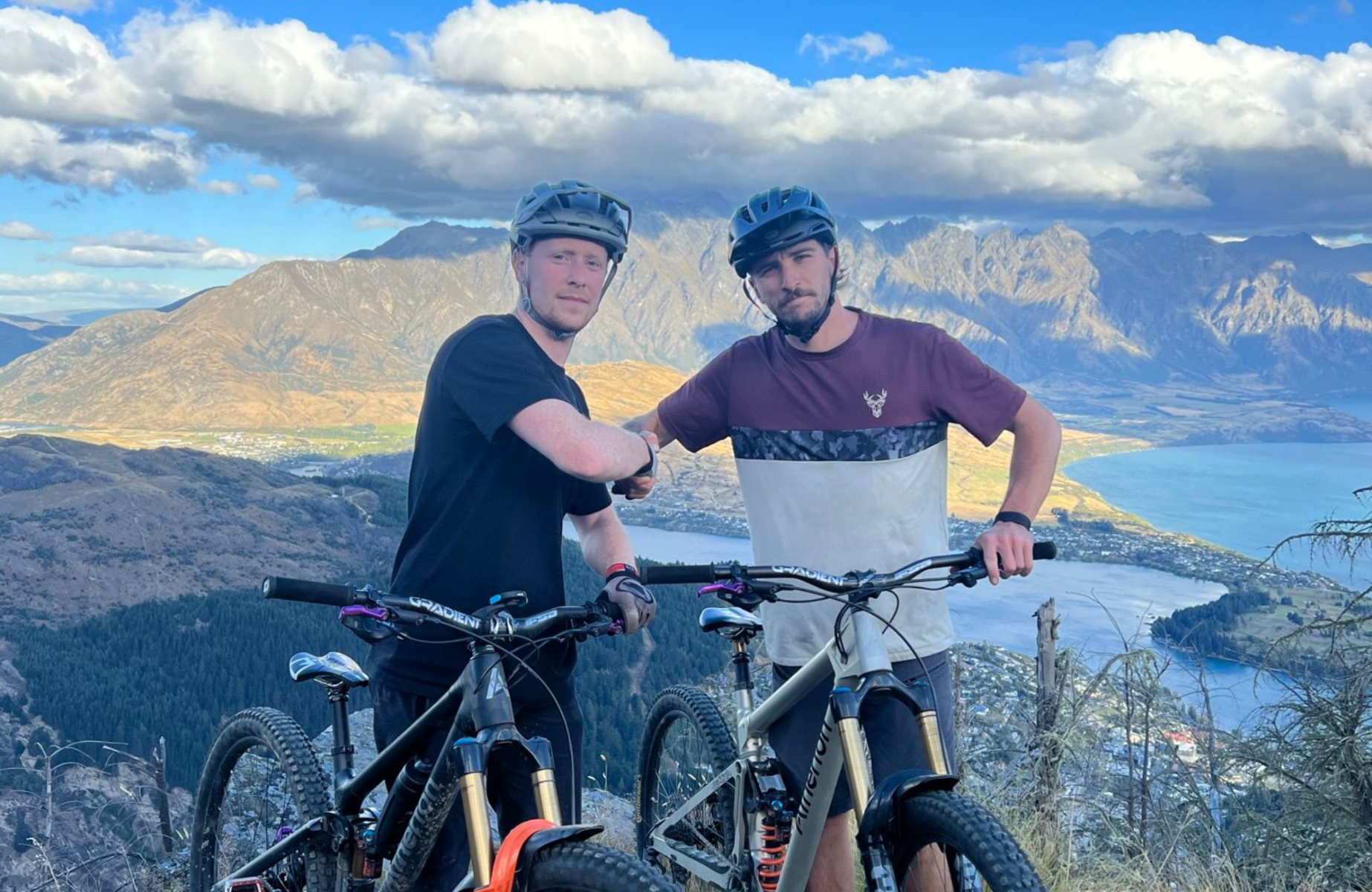
Honestly this whole process took longer than we thought but it was vital for us to be 100% confident before we moved to production. As the riders were testing we also collected lots of feedback on ride feel, Dan and Charlie’s feedback tempered with the views of lower capability riders to get to the perfect blend of Front and Rear compliance.
We’re a very small team and alongside the actual product we needed to develop systems for purchasing, manufacturing, waste management and so much more … Scott Aisthorpe, Will Carne, Will May-White and Chris Bailey, we couldn’t have done it without you.
More like this...
We rode with 40 Atherton Bikes owners from as far afield as Sweden, Switzerland, Germany and the USA. It was a day to celebrate our amazing customers who are the best ambassadors a brand could ever wish for and Dyfi delivered with blue skies and actual dusty trails!
We take our lifetime guarantee VERY seriously and we are well-known as the most uncompromising set of perfectionists you’re ever going to meet! So it goes without saying that the testing for our prototype bikes would be absolutely brutal for both man and machine!




